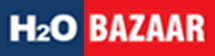
Microtorr is the dream of a technocrat entreprenuer Mr. R. Thiyagarajan, who tookup the challange of designing, fabricating and commissioning a "Thermovac Chamber" to test "Aryabhatta" India's first scientific satellite project in 1973. This was a pioneering effort where limited technology and vague specifications caused innumerable hurdles and the same were overcomed with true ingenuity.
The Thermovac Chamber was successfully commissioned in 1974 and launching of "Aryabhatta" put India on the map of spaceage nations.
Over the years Microtorr pioneered several developments in vacuum systems and related products which not only fulfilled the client's requirement but also saved the country precious foriegn exchange by means of import substitution.
Decades down the timeline Microtorr continues to serve several prestigious public sector, private sector commercial and research organizations with high technology vacuum systems, furnaces and related products tailored to suit their specific requirements.
Microtorr was established in the year 1973 by a dynamic technocrat entrepreneur Mr. R. Thiyagarajan to pioneer the manufacture of high quality vacuum systems, furnaces and accessories in India and save the country valuable foreign exchange otherwise spent on expensive imported equipment.
Microtorr became the first Indian company to manufacture the THERMOVAC Chamber to test ARYABHATTA Satellite in 1974 for Indian Space Research Organization (ISRO) then called The Indian Satellite Project. The Thermovac Chamber was commissioned at Bangalore. The pioneering effort of Microtorr in commissioning this project can be fathomed from the fact that no readymade technology was available in India then and the only vague specifications were provided to commence the work. Through sheer persistence and extensive research Microtorr was able to overcome hurdles of enormous magnitude and the successful launch of "ARYABHATTA" is now an important landmark in India's Scientific History.
The accomplishment of this challenging task clubbed with the satisfaction and appreciation expressed by such important a customer organization, boasted the morale and confidence at Microtorr. Later in the year 1984 Microtorr was entrusted with the complex responsibility of transplanting the entire thermo vacuum facility at ISRO from Peenya to New Space Application Centre Complex in Kodihalli, Bangalore. The Responsibility was not merely limited to transplanting the system but also to argument its capabilities by incorporating turbo molecular/Cryo pumps, installing liquid nitrogen vessels and liquid nitrogen and nitrogen vapour lines. The work was completed in a record time with complete customer satisfaction. In 1985-86 another Thermovac Chamber with a unique Cryo Panel design was commissioned at the Liquid Propulsion Systems Centre (LPSE) to test space sub-assemblies.
Absorbing Engineering and technological challenges, innovating designs, working in close coordinated teams and maintaining positive attitude at all times is a way of life at Microtorr which propelled it into a set of few companies which have access to and experience with exclusive technology in vacuum systems and furnaces. M/s. Leybold of Germany when contracted to manufacture and supply 80kg Twin Chamber Copper Melting Furnace to produce oxygen free high purity electronic grade copper for a prestigious Indian Research Organization selected Microtorr as its Indian partner to manufacture major components. Microtorr interacted with Leybolds for advance fabrication technology and successfully manufactured and supplied the required components under the partnership contract by meeting their stringent quality and test specifications
Microtorr have several first time projects in India to its credit in the field of Vacuum Systems and furnaces. A few among them are;
Fabrication of Electron beam Welding Chamber - a square chamber largest ever built in India weighing more than 25 tons.
Design, Fabrication and Installation of Vacuum Brazing Furnace with operating temperatures of 625 Deg C to a maximum of 800 Deg C and zone uniformity of +/- 3 Deg C for Vacuum Brazing of Aluminum Heat Exchangers in Aviation Industry. This know-how is available with few companies in the world. The product was well accepted and several exchangers were supplied with 98% success rate.
High Vacuum High Temperature Sintering Furnace with graphite heating elements capable of operating at temperature of 1450 Deg C was designed and supplied to R&D of a large public sector engineering company. This furnace is now in use for several years to manufacture Tungsten Graphite electrical contacts.
Furnace designed to anneal 3000 aneroids in a single batch. Aneroids are used in high altitude weather balloons sent up by meteorologists.
Design, Fabrication and Installation of High vacuum High Temperature Quenching Furnace for heat treating of garter springs used in Nuclear reactors. This is a unique twin chamber design isolated by a remotely operated gate valve, pusher rod and moving radiation shield to transfers material at the end of heating cycle from heating chamber to quenching chamber.
Oil Flow test rig. pressure flow test rig for Aircraft Engines.
High Vacuum High Pressure Controlled Atmosphere Furnace for DRML, Hyderabad. This is a unique furnace capable of operating under high vacuum of 10-6 mbar at a very high pressure of 150 psi. The key is to make a gate valve which works under this magnitude of vacuum and pressure.
Steel shell with appropriate ducting and blower for titanium sponge plant at DMRL, Hyderabad.
Bath Type Cryostat for BHEL R&D Centre, Hyderabad
80kg capacity twin chamber vacuum induction melting furnace for OFHC Copper in association with Leybold AG of Germany for NFTDC, Hyderabad.
Microtorr presently manufactures a wide range of high quality Vacuum Systems, Furnaces and related components to cater to diverse requirements in the customer industry and enjoys a high level of goodwill amongst its customers, suppliers, and associates
Mr Ramesh T.
Director
Plot No: P11/1, Road No: 14 I.D.A., Nacharam
Hyderabad,Andhra Pradesh,500076,IN.